Researchers have discovered that glass formed
in space has remarkable properties.
by Karen Miller and Dr Tony
Phillips
It's easy: mix together some materials
like sand, limestone and soda. Heat them above 2000o
F. Then cool the incandescent liquid carefully so that crystals
cannot form.
That's how you make glass.
Craftsmen on Earth have followed this basic
recipe for millennia. It works. "Now we know it works even better
in space," says glass and ceramics expert Delbert Day, who has been
experimenting with glass melts on space shuttles over the past twenty
years. Day is the Curators' Professor Emeritus of Ceramic Engineering
at the University of Missouri-Rolla.
Going into those first experiments, he says,
he expected to end up with a purer glass. That's because on Earth,
the melts--the molten liquid from which glass is formed--must be
held in some kind of container. That's a problem. "At high temperatures,"
says Day, "these glass melts are very corrosive toward any known
container." As the melt attacks and dissolves the crucible, the
melt--and thus the glass--becomes contaminated.
In microgravity, though, you don't need a container.
In Day's initial experiments, the melt--a molten droplet about 1/4
inch in diameter--was held in place inside a hot furnace simply
by the pressure of sound waves emitted by an acoustic levitator.
With that acoustic levitator, explains Day,
"we could melt and cool and melt and cool a molten droplet without
letting it touch anything." As Day had hoped, containerless processing
produced a better glass. To his surprise, though, the glass was
of even higher quality than theory had predicted.
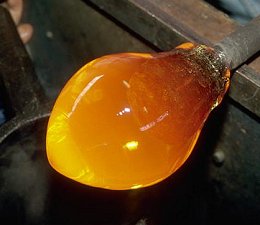
Copyright Dave Bartruff
A blob
of molten glass comes out of the fire at the Orrefors glassworks
in Sweden.
|
When most people think of glass, they
think of that transparent stuff in window panes. But glass doesn't
have to be transparent nor is it always found in windows. Among
researchers there's a different definition: "glass" is a solid material
with an amorphous internal structure. The atoms in solids are usually
arranged in regular, predictable patterns, like bricks fitted into
a wall. But if the atoms are just jumbled together in a disorganized
way, like bricks dumped on the ground... that's glass.
The window glass that we're so familiar with
is made mostly of silica--a compound of silicon and oxygen. It's
essentially melted sand. But in theory, a melt of any chemical composition
can produce a glass as long as the melt can be cooled quickly enough
that the atoms don't have time to hook themselves up into patterns,
or crystals.
In Earth-orbit, it turns out, these molten liquids
don't crystallize as easily as they do on Earth. It's easier for
glass to form. So not only can you make glass that's less contaminated,
you can also form it from a wider variety of melts.
But why is that important? What's wrong with
glass made of silica?
For windows silica is just fine. But glass made
from other chemical compositions offers a panoply of unexpected
properties. For example, there are "bioactive glasses" that can
be used to repair human bones. These glasses eventually dissolve
when their work is done. On the other hand, Day has developed glasses
which are so insoluble in the body that they are being used to treat
cancer by delivering high doses of radiation directly to a tumor
site.
Another example: Glass made of metal can be
remarkably strong and corrosion-resistant. And you don't need to
machine it into the precise, intricate shapes needed, say, for a
motor. You can just mold or cast it.
Also intriguing to space researchers is fluoride
glass. A blend of zirconium, barium, lanthanum, sodium and aluminum,
this type of glass (also known as "ZBLAN") is a hundred times more
transparent than silica-based glass. It would be exceptional for
fiber optics.
A fluoride fiber would be so transparent, says
Day, that light shone into one end, say, in New York City, could
be seen at the other end as far away as Paris. With silicon glass
fibers, the light signal degrades along the way.

more
Steel balls
bounce on flat plates of titanium alloy, metallic glass,
and stainless steel. The ball bouncing on metallic glass
keep going for a remarkably long time.
|
Unfortunately, fluoride glass fibers are very
difficult to produce on Earth. The melts tend to crystallize before
glass can form.
The reason, says Day, is that gravity
causes convection or mixing in a melt. In effect, gravity "stirs"
it, and, in a process known as shear thinning, the melt becomes
more fluid. This same process works in peanut butter: the faster
you stir it, the more easily it moves.
In melts that are more fluid, like those stirred
by gravity, the atoms move rapidly, so they can get into geometric
arrangements more quickly. In thicker, more viscous melts, the atoms
move more slowly. It's harder for regular patterns to form. It's
more likely that the melt will produce a glass.
In microgravity, Day believes, melts may be
more viscous than they are on Earth.
While this theory has not yet been confirmed,
some experimental results suggest that it is correct. NASA researcher
Dennis Tucker worked with fluoride melts on the KC-135, a plane
that provides short bursts of near zero-gravity interspersed with
periods of high gravity.
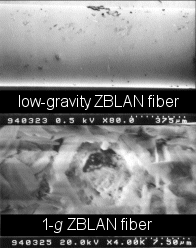
more
The surfaces
of ZBLAN fibers formed in near-weightlessness (upper panel)
and in normal Earth-gravity (lower panel).
|
"He did some glass-melting experiments,
trying to pull thin fibers out of melts," recounts Day. "During
the low-gravity portion of the plane's flight, when g was
almost zero, the fibers came out with no trouble. But during the
double-gravity portion of the plane's flight, the fiber that he
was pulling totally crystallized."
That result, says Day, could be explained
by shear thinning. "A melt in low gravity doesn't experience much
shear. But as you increase g, there'll be more and more movement
in the melt." Shear stresses increase. The effective viscosity of
the melt decreases. Crystallization becomes more likely.
Day is currently planning
his next experiment in space--onboard the International Space Station--which
he hopes will confirm his ideas. He'll be melting and cooling identical
glass samples in the same way on Earth and in microgravity. Then
he'll count the number of crystals that appear in each sample. If
shear-thinning exists, he says, there will be fewer crystals in
the space-melted samples than in the ones produced on Earth.
Eventually, Day hopes to take these lessons
learned from space and apply them to glass production on the ground.
Metallic glasses. Bioactive glasses. Super-clear fiber optics. The
possible applications go on and on.... which makes the value of
this research crystal clear.
|